1.-
Enunciado del problema
2.- Regímenes de trabajo
3.- Material de los
electrodos
4.- Reglaje del generador
5.- Elección de la limpieza
6.- Recapitulación de
datos
7.- Dimensionamiento
de los electrodos
8.- Cálculo del
tiempo de mecanizado
9.- Conclusiones
10.- Controles a realizar
1.-
Enunciado del problema
Se trata de realizar
un agujero pasante rectangular de 21 x 14 mm, según la Fig. E2.1,
con las condiciones siguientes:
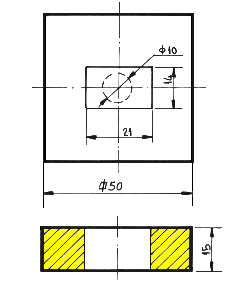 |
|
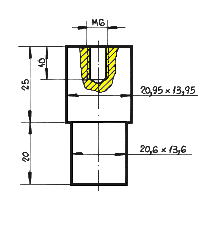 |
Fig. E2.1
PIEZA |
|
Fig. E2.2
ELECTRODO |
-
Acabado con rugosidad media menor
de 2 µm.
-
Material de la pieza: F-521 templado.
Dureza 63 Rc.
-
Número de piezas: 1.
-
No habrá pulido posterior.
-
No tiene importancia la conicidad
que pueda darse en el proceso.
-
Se realizará un pretaladrado de
Ø 10 mm antes de templar.
-
Los electrodos de desbaste y acabado
se realizarán en una sola pieza, en Cu, escalonados (Fig.
E2.2).
2.-
Regímenes de trabajo
Dadas las posibilidades
de la máquina no pueden realizarse más que dos regímenes: Desbaste y acabado.
3.-
Material de los electrodos
El enunciado del problema
obliga a que los electrodos sean de cobre. No obstante la rugosidad media
final requerida, debe de ser menor de 2 µm (Nr: 24-27), lo que exigiría
que el electrodo de acabado fuese de cobre, siempre que se tratara de
escoger entre grafito y cobre.
4.-
Reglaje del generador
-
Polaridad.- Al
tratarse de una pareja cobre-acero, la polaridad del electrodo debe
de ser positiva.
-
Niveles de intensidad y
excitación.-
Desbaste. La superficie frontal en desbaste será:
SD = 21 x 14
- p 102 / 4 = 215,5 mm2
Ello quiere decir que se puede agotar la máxima
potencia de la máquina A-118 en el nivel de intensidad 4 y punto de
excitación 4, que exige una superficie mínima de 200 mm2
(tabla A4.4).
Acabado. Se debe de obtener una rugosidad media menor de 2 µm, o lo
que es lo mismo una rugosidad total de aproximadamente 8 µm. Mirando
en las tablas se observa que esto se puede conseguir con uno de los
regímenes siguientes:
|
Nivel |
Excitación |
ti |
Smín.
(mm2) |
Arranque VW
(mm3/min) |
Desgaste
o/o |
1.- |
1 |
2 |
5 |
- |
0,4 |
5 |
2.- |
1 |
3 |
4 |
10 |
1,2 |
3 |
3.- |
2 |
3 |
1 |
20 |
3 |
20 |
El primero de ellos
tiene la pega de que será excesivamente lento y la ventaja de que es
el único con el que se tiene la seguridad de que se obtendrá la rugosidad
deseada.
El segundo requiere una superficie mínima de 10 mm2
y es probable que esta circunstancia no se de, con lo cual el arranque
será menor, el desgaste mayor y la rugosidad puede ser otra.
En cuanto al tercero será imposible aplicarlo, ya
que requiere una superficie mínima de 20 mm2.
En principio tomaremos el primero, aunque en la práctica
se podría tomar el segundo y el tiempo de acabado se dividiría por 3
aproximadamente.
-
Tiempo de impulso.-
Desbaste. Dado que se trata de un agujero pasante y de una sola pieza
a realizar, se realizará de forma que se obtenga un máximo arranque,
aún a costa de un mayor desgaste. Por ello en este caso ti : 9 (Tabla
A4.4).
Acabado. Tabla A1.2. El acabado requerido se obtiene con ti : 5, aunque
este punto presenta un gran desgaste volumétrico relativo (sV : 5 por 100).
5.-
Elección de la limpieza
El enunciado del problema
dice que no importa el que se produzca cierta conicidad. Por ello se puede
realizar la limpieza por presión o aspiración a través de la pieza, aprovechando
el pretaladrado de Ø 10 mm. Con el fin de comprobar las diferencias se
pueden realizar con el mismo electrodo dos ejercicios, uno con limpieza
por aspiración y otro con limpieza por presión. La presión del manómetro
se graduará de forma que el trabajo sea estable.
6.-
Recapitulación de datos
En la ficha de trabajo
de este caso particular no se han rellenado los apartados correspondientes
a limpieza, por lo dicho en el apartado anterior.
ELECTROEROSION
FICHA DE TRABAJO
EJERCICIO NUMERO 2
|
Datos
del problema |
Electrodo núm. |
1 |
2 |
2' |
. |
Operación (Desbaste: D, Acabado: A) |
D |
A |
A |
. |
Material electrodo |
E-Cu |
E-Cu |
E-Cu |
. |
Material pieza |
F-521
temp. |
F-521
temp. |
F-521
temp. |
. |
Número de piezas a realizar |
1 |
1 |
1 |
. |
Estado superficial deseado (Nr) |
- |
24-27 |
24-27 |
. |
Rugosidad total (µm) |
32 |
75 |
.
|
. |
Reglaje
Generador |
Polaridad electrodo |
. |
. |
. |
. |
Nivel intensidad Excitación |
4.4 |
1.2 |
1.3 |
. |
Tiempo impulso Puntos (ti) |
9 |
5 |
4 |
. |
Tiempo pausa Puntos (to) |
2 |
2 |
2 |
. |
K.C. Puntos |
7 |
7 |
7 |
. |
Limpieza |
Forma |
. |
. |
. |
. |
Presión (bar) |
. |
. |
. |
. |
Datos
para cálculos |
Menor medida por lado (mm) |
0,202 |
- |
0,076 |
. |
Espacio entre electrodo y pieza (mm) |
0,082 |
0,026 |
0,03 |
. |
Desgaste volumétrico relativo sV
(o/o) |
2,5 |
5 |
3 |
. |
Arranque Vw (mm3/min) |
96 |
0,4 |
1,2 |
. |
Superficie mínima (mm2) |
200 |
- |
10 |
. |
Superficie a trabajar (mm2) |
215,5 |
7,5 |
7,5 |
. |
Volumen a arrancar (mm3) |
3233 |
112,5 |
112,5 |
. |
Estimación tiempo mecanizado (min) |
34' |
281'
Total =
315' |
94'
Total =
128' |
. |
Resultados
finales |
Tiempo real de mecanizado (min) |
. |
. |
. |
. |
Superficie obtenida (Nr) |
. |
. |
. |
. |
Observaciones |
. |
. |
7.-
Dimensionamiento de los electrodos
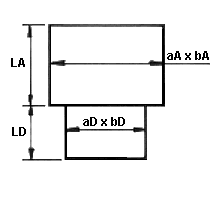 |
Fig. E2.3 |
Sin pulido posterior
las dimensiones deberán de ser:
Electrodo de desbaste
aD = 21 - 2 x 0,202
= 20,596 mm
bD = 14 - 2 x 0,202
= 13,596 mm
Se puede realizar el electrodo de 20,6 x 13,6 sin incurrir
en errores.
Electrodo de acabado
aA = 21 - 2 x 0,026
= 20,948 mm
bA = 14 - 2 x 0,026
= 13,948 mm
Se realizará el electrodo de 20,95 x 13,95.
En cuanto a la longitud
de los electrodos se puede indicar lo siguiente: La longitud de desbaste
(LD) deberá ser mayor de 15 mm al ser el electrodo escalonado.
En cuanto a la longitud del electrodo de acabado (LA) será
de 25 mm porque como el desgaste es grande, el desgaste lineal también
lo será. Si en la fase de acabado se pasa toda la longitud de electrodo,
se asegurará que toda la longitud del agujero tenga las medidas dadas,
y que el radio de las esquinas sea lo menor posible.
8.-
Cálculo del tiempo de mecanizado
-
Desbaste
- Superficie frontal: SD = 210,5 mm2
- Volumen a arrancar: VD = 210,5 x 15 = 3233 mm3
- Arranque de material (tabla A4.4): VW = 96 mm3/min.
- Tiempo de mecanizado en desbaste: tD = 3233/96 = 33,68
min; tD ~ 34 min.
-
Acabado
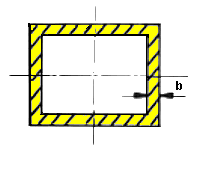 |
Fig. E2.4 |
La superficie frontal
(área rayada Fig. E2.4), corresponde a una banda
cuya longitud es el perímetro y cuya anchura "b" se calcula
con la fórmula:
b = MmlD - gD -
( RtD - RtA ) / 2
b = 0,202-0,082-(0,032-0,0075)/2 = 0,10775 mm
Perímetro, p = (21 + 14) 2 = 70 mm
- Superficie frontal en acabado: SA = p.b
SA = 70 x 0,10775 = 7,5
mm2
- Volumen a arrancar: VA = 7,5 x 15 = 112,5 mm3
- Arranque de material (tabla A1.2): VW = 0,4 mm3/min.
- Tiempo de acabado, tA = 112,5 / 0,4 = 281 min.
- Tiempo total de mecanizado, tM = 34 + 281 = 315 min
= 5h 15 min
9.-
Conclusiones
La condición de que
el acabado final se ha de realizar con una rugosidad media muy pequeña
lleva consigo un gran aumento en los tiempos de mecanizado.
Si se escoge el otro régimen (Nivel 1, Exc 3 y ti 4),
aunque la superficie en régimen de acabado no llegue hasta los 10 mm2
los resultados serían:
- Dimensiones del
electrodo: 20,94 x 13,94 mm
- Superficie a trabajar: 7,5 mm2
- Volumen a arrancar: 112,5 mm3
- Tiempo de acabado: tA = 112,5 / 1,2 =
94 min
- Tiempo total: tM = 128' = 2h 8 min
El resultado será
algo mayor debido a la dificultad ya mencionada.
10.-
Controles a realizar
-
Tiempo de mecanizado.-
Se debe de comprobar que si el ejercicio se realiza con limpieza por
aspiración, el arranque es algo mayor que si se realiza con presión,
y por tanto es menor el tiempo de mecanizado.
-
Desgaste lineal.-
Se debe de observar la forma en que quedan los electrodos después
del mecanizado, principalmente el de acabado.
-
Comprobar la conicidad,
tanto si se ha realizado el ejercicio con limpieza por presión como
por aspiración.
-
Rugosidad final,
principalmente en el caso de que se escoja el segundo régimen de acabado
expuesto.
[ Anterior | Siguiente | Arriba ]
|